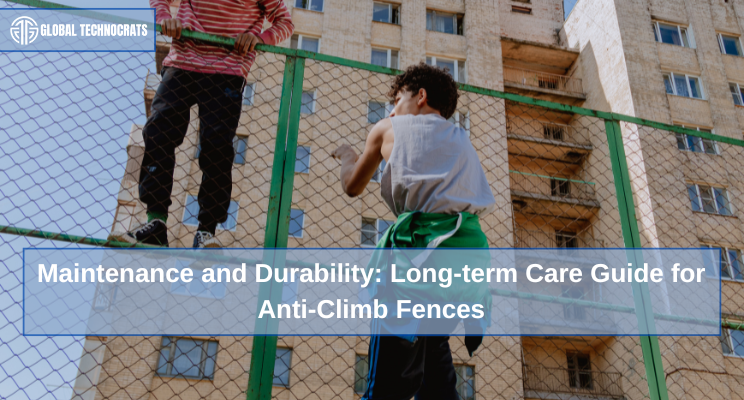
Table of Contents #
- Introduction
- Preventive Maintenance Schedules
- Environmental Impact Management
- Repair Procedures
- Coating Maintenance
- System Testing and Validation
- Documentation and Compliance
- FAQs
- Conclusion
Introduction #
Proper maintenance of anti-climb fencing systems is crucial for ensuring long-term security effectiveness. According to BIS guidelines (IS 16432-1:2014), regular maintenance can extend system lifespan by up to 40% while maintaining optimal security performance. This guide outlines comprehensive maintenance procedures and durability considerations.
Preventive Maintenance Schedules #
Regular Inspections #
Per ISO 9001:2015 maintenance protocols:
1. Visual Inspections
- Frequency: Monthly
- Check points:
- Fence alignment
- Post stability
- Wire tension
- Connection integrity
2. Structural Assessment
- Frequency: Quarterly
- Components:
- Foundation stability
- Post anchoring
- Panel connections
- Security fixtures
Technical Audits #
According to maintenance standards:
1. Security Features
- Frequency: Bi-annual
- Verification of:
- Anti-climb mechanisms
- Tamper-proof fixtures
- Security bolts
- Integration systems
2. System Testing
- Frequency: Annual
- Testing of:
- Electronic components
- Detection systems
- Access controls
- Emergency features
Environmental Impact #
Management #
Climate-Specific Maintenance #
Based on BIS environmental guidelines:
1. Coastal Areas
- Salt spray inspection
- Corrosion monitoring
- Protective coating checks
- Hardware assessment
2. Industrial Zones
- Chemical exposure checks
- Pollution impact assessment
- Material degradation monitoring
- Enhanced cleaning protocols
Weather Protection #
Following IS 4759 specifications:
1. Monsoon Preparation
- Drainage inspection
- Rust prevention
- Foundation stability
- Water accumulation prevention
2. Summer Maintenance
- Expansion joint checks
- UV damage assessment
- Coating integrity
- Hardware tightening
Repair Procedures #
Minor Repairs #
Standard repair protocols include:
1. Panel Repairs
- Mesh straightening
- Wire replacement
- Joint reinforcement
- Surface treatment
2. Hardware Maintenance
- Bolt tightening
- Hinge lubrication
- Lock mechanism service
- Anti-tamper device checks
Major Repairs #
According to structural repair guidelines:
1. Post Replacement
- Support installation
- Foundation repair
- Alignment verification
- Connection restoration
2. Panel Replacement
- Section isolation
- Security maintenance
- Installation verification
- System testing
Coating Maintenance #
Protective Coating Systems #
Per IS 4759 requirements:
1. Galvanized Surfaces
- Zinc coating inspection
- Touch-up procedures
- Thickness measurement
- Adhesion testing
2. Additional Coatings
- Paint system checks
- Powder coating maintenance
- Anti-corrosion treatment
- UV protection renewal
Restoration Procedures #
Following coating maintenance standards:
1. Surface Preparation
- Cleaning protocols
- Rust removal
- Surface profiling
- Moisture control
2. Coating Application
- Material selection
- Application methods
- Curing requirements
- Quality control
System Testing and Validation #
Security Verification #
According to MHA guidelines:
1. Physical Security
- Climb resistance testing
- Cut resistance verification
- Impact resistance
- Structural integrity
2. Integrated Systems
- Sensor functionality
- Alert system testing
- Communication checks
- Response verification
Performance Validation #
ISO 9001:2015 requirements specify:
1. Documentation
- Test records
- Maintenance logs
- Repair history
- Inspection reports
2. Certification
- Compliance verification
- Standard adherence
- Performance metrics
- Safety validation
Documentation and Compliance #
Maintenance Records #
Per regulatory requirements:
1. Regular Documentation
- Inspection reports
- Maintenance activities
- Repair records
- Testing results
2. Compliance Reports
- Standard adherence
- Certification status
- Regulatory compliance
- Safety verification
Asset Management #
Following facility management standards:
1. Inventory Control
- Component tracking
- Spare parts management
- Tool maintenance
- Material storage
2. Resource Planning
- Maintenance scheduling
- Personnel allocation
- Budget management
- Equipment tracking
FAQs #
Q: How often should anti-climb fencing be inspected in industrial areas? A: Monthly visual inspections and quarterly structural assessments per ISO 9001:2015 protocols.
Q: What is the recommended frequency for coating inspection in coastal areas? A: Bi-monthly inspections with quarterly coating assessments per IS 4759 guidelines.
Q: How should emergency repairs be documented? A: Immediate incident reporting followed by detailed repair documentation per regulatory requirements.
Conclusion #
Effective maintenance and durability management of anti-climb fencing systems requires systematic approach, regular monitoring, and proper documentation. Following these guidelines ensures optimal security performance and extended system lifespan.
References #
- Bureau of Indian Standards (2014) “IS 16432-1:2014”
- IS 4759 “Hot-dip zinc coatings specifications”
- ISO 9001:2015 “Quality Management Systems”
- Ministry of Home Affairs “Security System Maintenance Guidelines”
- Facility Management Standards 2023
- Industrial Safety Regulations 2023